Metal diaphragms are plates of metal built to axially deform and regulate pressure. Various systems across industries use the diaphragms to separate opposing fluids, regulate or cap pressure levels, indicate when pressure levels reach above certain thresholds, and more. For example, food processing, pharmaceutical production, and semiconductor manufacturing all rely on well-constructed metal diaphragms to control dynamic systems. But in each application, the material plays a large role in the diaphragm’s performance.
Keep reading to learn more about the metal diaphragm production process made and choosing an ideal metal material for your specific application.
How are Metal Diaphragms Manufactured?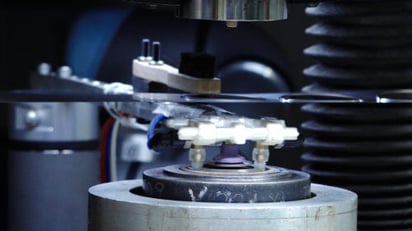
Metal diaphragm manufacturers incorporate multiple steps into production based on the specifications of the product and details of the application. The diaphragm’s required life cycle, deflection ability, and ability to withstand pressure all influence the profile shape and material selection.
Manufacturers will digitally design and virtually test a diaphragm model in advance of production to solve functionality and manufacturability issues. Creating a computer-aided design (CAD) file allows the design engineer to check for potential flaws before physical prototyping. Based on the specifications of the application, the design engineers will consider the following:
Solid Centers
There are two main types of solid center diaphragms: high-sensitivity low-pressure (HSLP) diaphragms and low-sensitivity high-pressure (LSHP) diaphragms. HSLP diaphragms are often matched with pressure sensors to detect potential fluid breaches and contamination in food, beverage, and pharmaceutical production. LSHP diaphragms typically see use as a failsafe component, as these diaphragms withstand high pressure levels and only open when pressure levels reach a predetermined range.
Selecting a Profile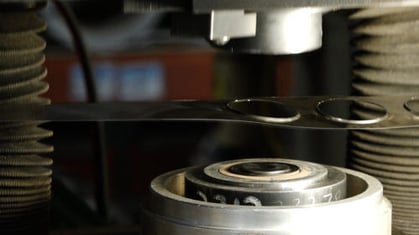
Metal diaphragms may be domed, corrugated, or flat. Flat metal diaphragms are the easiest to mass produce, but corrugated diaphragms are popular for their linear characteristic curve and ability to deform to a greater degree without incurring damage. The linear curve gives the diaphragm extended range, high sensitivity, and better spring rates. Designers may choose to enhance or modify certain characteristics by specifying the material thickness and the depth or pitch of the corrugation. These features will influence the overall operating life of the diaphragm.
Once the design is complete, diaphragms get produced through metal stamping. Metal stamping processes use a die (or a series of dies) that press into and deform metal stock into the preferred shape. After metal stamping, the completed diaphragms are quite delicate. Manufacturers need to carefully package the items to protect them during storage or shipping.
Read more about our corrugated diaphragm capabilities here.
Choosing a Diaphragm Material
Different metals offer different characteristics and advantages. Some of the most commonly used metals used for diaphragms include:
- Inconel®. This material resists abrasion, corrosion, and heat. It retains its characteristics in temperatures above 750°F.
- Haynes® 242®.Haynes 242 is highly ductile and resists thermal expansion up to temperatures of 1,600°F.
- Hastelloy®. Hastelloy features excellent corrosion resistance, tolerates exposure to most chemicals, and can operate at high temperatures for limited periods.
- Titanium. Titanium nitride offers good resistances to abrasion and adhesion, while titanium aluminum nitride diaphragms provide excellent resistances to both.
- Monel®. This material offers good resistance to saltwater and high resistance to corrosion under exposure to non-oxidizing acids.
- 17-7 PH stainless steel. This stainless steel alloy features superior strength and hardness, resists deformation and fatigue, and offers good corrosion resistance.
The appropriate material selection will depend heavily on the intended use case, including the process fluids the diaphragm may come into contact with, operating temperature ranges, and various environmental factors.
To learn more about the materials listed above, read our Choosing Materials Guide.
Diaphragm Manufacturing Considerations
When designing or ordering custom metal diaphragms, pause to consider the various options at each production stage to ensure an optimal solution.
- Design and engineering. During this stage, make detailed CAD files and 3D mockups before physical prototyping begins so the designs can be thoroughly tested and optimized.
- Stamping process. During the metal stamping process, manufacturers can control camber, concentricity, and other factors. Depending on your intended application, you may have unique requirements for the edge burr and tolerance threshold.
- Tooling. Consider how different tooling processes, such as metal-to-rubber or metal-to-metal, will influence production costs, as well as the final product and its performance in the end application. We offer custom tooling, made in-house in our tool room, to all of our clients.
- Packaging. Be sure that the packaging accounts for the fragility of metal diaphragms.
Metal Stamped Diaphragms from Hudson Technologies
Selecting the right material for your metal diaphragms is crucial for ensuring the proper performance of your equipment. At Hudson Technologies, we have the experience and expertise to design and create metal diaphragms for any industrial use case. To see how our capabilities can benefit your operation, please contact us today.